A revolutionary software solution
When cooling down from the melt phase to room temperature, PEEK shrinks about 3.5%. This means a printed track which 100 mm long typically wants to shrink to 96.5 mm, where applications typically require a geometric error a few tenths of millimeters.
To some extent, a linear expansion of the 3D model in X, Y and Z direction helps to compensate the errors a little bit, but this method typically requires multiple iterations, and it does not resolve local warpage of products. Therefore, it is not sufficient to meet the accuracy requirements for most applications.
The standard routes to overcome this is to print slowly crystallizing materials such as PEKK, to add carbon fibres to reduce shrink, or to cool down the material quickly in the printer and recover crystallinity by an additional thermal treatment. None of these avenues offer the ability to print accurate products with the native properties of pure PEEK.
Bond3D, together with partner AniForm, have developed unique software to calculate local shrink and warpage during printing, and locally compensate the toolpaths of printed tracks in X, Y and Z direction in a way that the final product meets or even exceeds accuracy requirements.
The solution is revolutionary in that in fact a product with a warped shape is printed, which after cooling down to room temperature results in a part which accurately conforms to the intended shape.
Printed tracks are modified in all directions, implying that printed slices are no longer flat.
Bond3Ds software is unique
This software enables Bond3D to print one of the most difficult polymers in the world (PEEK) with an accuracy exceeding that of the world market leader with an amorphous material (amorphous means no crystals are formed during cool down, and therefore shrink is quite limited).
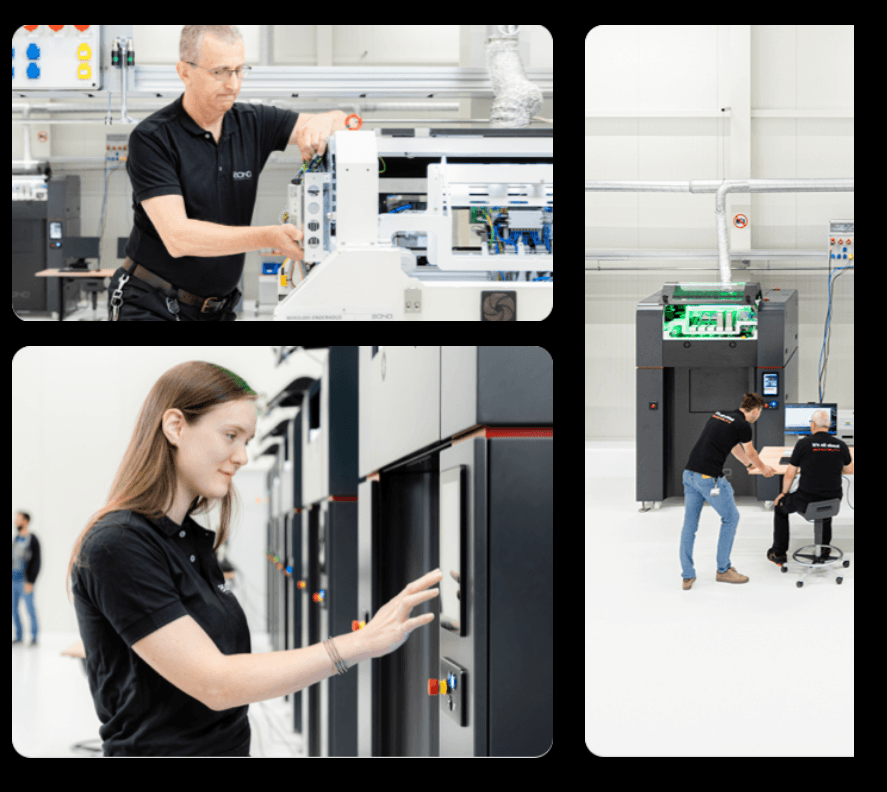
The best possible accuracy
This software enables Bond3D to print large parts from high performance polymers with an accuracy greater than what is possible with other additive manufacturing technologies, and even better than injection moulding.
The patented voidless printing technology that Bond3D has developed already allows to post process printed parts without exposing internal voids to the surface, an important limitation of conventional FDM. Post processing can be deployed by printing functional surfaces in a near-net shape fashion, and then subsequently use post processing techniques such as machining or polishing to improve accuracy or roughness of these surfaces to achieve the required properties.
Benefits of shrink compensation software
• Less need for post processing
More parts can be printed without the need of post processing, since the required accuracy is already met without post processing. Therefore, costs of printing additional material and cost of subsequently removing that material can be saved
• Complex internal geometries
Complex internal geometries, where post processing is not possible due to the limited access for tooling can be printed with the required accuracy where this was not possible before
• Design iterations
Fewer design iterations are needed, since the first print is usually within the required tolerances.
A game changer in the 3D printing industry
Shrink compensation software has emerged as a game-changer in the 3D printing industry, addressing the challenge of shrinkage during the cooling process and offering significant benefits across various aspects of manufacturing.
Cost benefit
Having to print less printing material and doing less post processing saves printing material, printing time and processing costs. Additionally, fewer design iterations are needed to arrive at the correct print recipe. Finally, the yield of the printers increases, since printed tracks are printed on the correct location, taking into account shrink and warpage of the underlying structure at the moment of printing the tracks.
Time benefits
Where previously multiple design iterations were required to approximately arrive at an optimal linear shrink percentage, the design is now often first time right. Since large parts can typically take up to tens of hours to print, saving design iterations considerably reduces the lead time of a new design.
Material processing benefits
As mentioned much less post processing or no post processing at all is required to obtain a part with the desired accuracy.
Environmental impact
Near-net shape printing material that does not have to be printed saves waste.
Business impact
The shrink compensation software reduces lead time and costs of new designs.
Our roadmap for further development
Bond3D has a roadmap to add further functionality to improve the shrink compensation software and expand its possibilities towards more complexity and higher accuracy.
Flowchart of conventional solution

Principle of the new solution
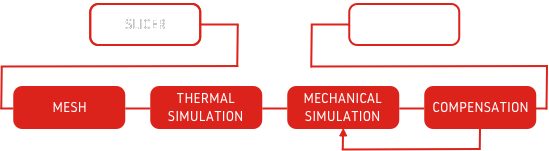
Intermediate results
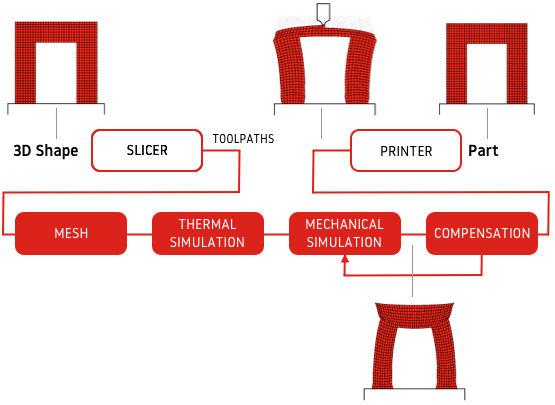
Talk to us
We believe transforming manufacturing is a team effort. Let’s get in touch and discuss how we can help you take the next step.