Why choose PEEK for additive manufacturing?
- Excellent wear properties
- Electrically insulating
- Easy post-processing
- Extreme temperatures (-40°C to +250°C)
- Mechanical strengths (TS 98 MPa)
- Chemical resistance (also sterilization by Gamma)
- Bio inert(also radiolucent for X-ray, CT or MRI)
- High purity
Pressure-controlled printing with PEEK
At Bond3D, we decided to follow the reverse strategy and adapt the process to the material, to preserve its favorable properties in printed products. In principle this could be any material, but we put the focus on high-performance polymers such as PEEK. Our ambition was to develop a printer that produces functional parts, not just prototypes, with properties that approach bulk values, concerning yield strength, leak tightness, chemical resistance, etc. To that end, we invented a technology called pressure-controlled printing.
The perfect extrusion
The conventional FDM (fused deposition modeling) process works with flow control of the molten material to be printed. Due to the natural variability of process conditions this can lead to over- or underextrusion: either too much or little material will be printed. Overextrusion can end disastrously and result in the loss of a print job, so underextrusion is generally preferred to create a safety margin. This, however, will result in voids in the printed product, as visualized by microscopy of a cross-section of the product. As a result, product density and strength are reduced as compared to bulk material values. For example, the interlayer bond strength, which determines the so-called z-strength, may be limited to 40%. When parts are exposed to a load in the vertical direction, they will crack prematurely, which is of course undesirable.
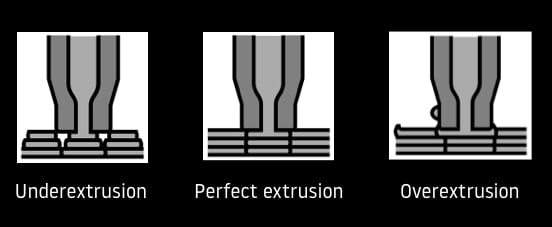
Bondability
With our solution, pressure control of the dispense rate, the molten material will flow until the gap between previously printed tracks is completely filled. This point is reached when the pressure level in the ‘melt pool’ – as measured from the vertical force it exerts on the print nozzle – indicates that no more material can be added. Then adjoining lines have bonded completely; we call this bondability, hence our company name. We can switch the control strategy between the conventional flow-controlled printing and the innovative pressure-controlled printing. After two tracks have been printed in flow control, pressure control can take over to fill the gap between these tracks completely.
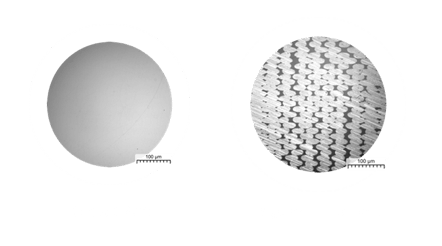
Voidless parts
When you now look at a cross-section of the printed product, you will see a solid, voidless part. An additional benefit is that our printed products are isotropic in strength, i.e., in all directions they have the same – favorable – properties, close to bulk datasheet values. We have demonstrated this for a complex manifold that was exposed to a leak test; the leak rate was found to be below the detection limit, at helium leak tightness level. Another printed product was subjected to an internal load in a burst pressure test. Again, the relevant property, the strength, was found to have a near-datasheet value. Just like bulk PEEK, our printed PEEK products are high-vacuum compatible, as validated by total organic content and residual gas analysis tests.
PEEK is high in strength
As a bonus, PEEK’s high strength in combination with its high ductility can be beneficial in many applications. We successfully demonstrated this for a printed back-up sealing ring, which during installation had to be stretched and twisted in order to put it on a shaft.
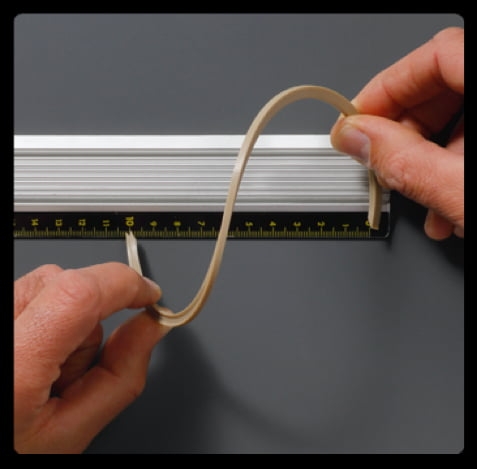
All our PEEK parts have excellent mechanical properties
To conclude, our patented technology enables printing of complex, functional parts made of PEEK with excellent mechanical properties, in all directions. The Bond3D process uses native materials, which allows for engineering with known materials without the usage of additives. If you need high-performance products with isotropic, voidless and native material properties, please get in touch. We can help to ‘upgrade’ your product design to PEEK printability in order to enhance functionality and performance.