Cranial implant (CMF)
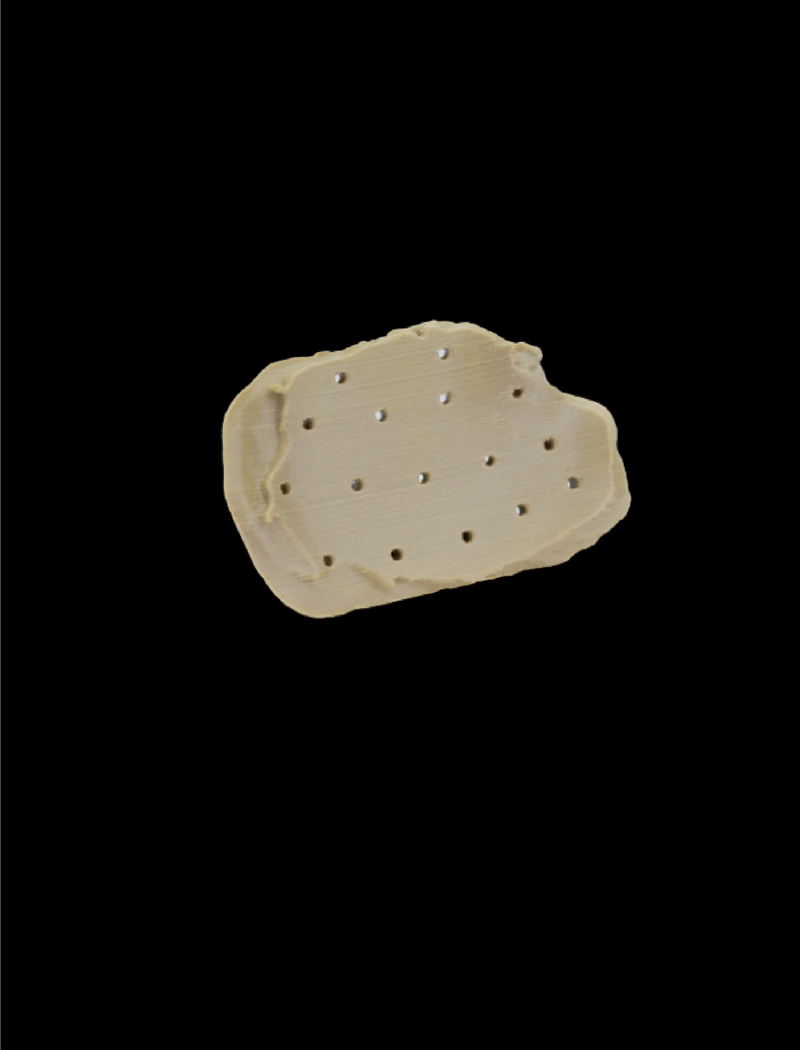
Patients are aging, staying longer active and demanding more quality of life than ever before. A wide range of medical procedures are required to address this shifting demand. High performing polymers are crucial to fulfill these needs. Ranging from sterilizable materials applied in endoscopy applications, to actual implants, or dental restorations, high performing polymers such as PEEK will play a significant role in this industry.
Bond3D adds a significant opportunity fulfilling the needs in these medical markets. For the first time a 3D printing process can deliver full functional performing materials to these applications. Designs can be integrated or feature advanced bone optimized in-grow structures for PEEK medical products.
The US aerospace industry first created polyetheretherketone, or PEEK, in the late 1970s after becoming interested in its high-temperature stability and subsequent potential for high-load, high-temperature applications. PEEK-OPTIMA, a highly pure and implantable grade of PEEK, was introduced to the market by Invibio Biomaterial Solutions in the late 1990s and quickly adopted by the medical device sector. Since that time, the use of medical-grade PEEK has multiplied.
Implantable PEEK is now widely used by medical device manufacturers to increase the biocompatibility of load-bearing implants. Compared to metal implants, it makes implants much more bone-friendly and is also much more compatible with diagnostic imaging.
In the 1980s, PEEK was first used in experimental medical devices. In the 1990s, clinical research led to widespread clinical acceptance, particularly in the area of spine implants. PEEK is steadily replacing current biomaterial standards in a variety of implant applications.
Today’s implantable PEEK polymers come in a variety of formulations, from unfilled grades with varying molecular weight to image-contrast and carbon fiber-reinforced grades. All are produced in accordance with strict quality standards and are supported by full raw material traceability. PEEK-OPTIMA, the first implantable unfilled PEEK polymer, was developed by Invibio Biomaterial Solutions in 1999. In 2007, image-contrast grades and carbon fiber-reinforced variants of the material (which offer significantly increased strength and stiffness) were introduced.
There are several benefits to using medical-grade PEEK in medical implants and devices. Some of these benefits include:
Medical-grade PEEK has several advantages over other materials commonly used in the healthcare industry.
We believe transforming manufacturing is a team effort. Let’s get in touch and discuss how we can help you take the next step.